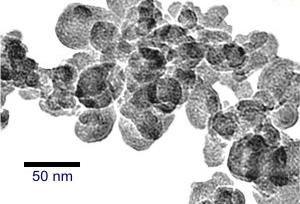
Diesel engines are widely used in mining operations because of their high-power output and mobility. Many mine operators prefer diesel-powered machines because they are more powerful than most battery-powered equipment and can be used without electrical trailing cables which can restrict equipment mobility. Also, available data strongly support the use of diesel equipment underground in coal mines for improved safety and productivity. Trolley wire haulage and other electric hazards such as batteries and battery charging stations could be avoided by using properly designed diesel equipment. With the continual expansion of the use of diesel engines in the mining industry and the uncertainties associated with the long-term effects of exhaust emissions on miners’ health, MSHA began assessing diesel particulate levels in underground mines in 1989.
DPM is a component of diesel exhaust (DE) that includes soot particles made up primarily of carbon, ash, metallic abrasion particles, sulfates, and silicates. Diesel soot particles have a solid core consisting of elemental carbon, with other substances attached to the surface, including organic carbon compounds known as aromatic hydrocarbons. Equipment used in mines are equipped with diesel engines. Consequently, miners in the vicinity of diesel-powered equipment may be exposed to DE/DPM.
Health effects of DE/DPM – The complexity of the chemical and physical composition of diesel exhaust emissions makes the assessment of health risk from exposure to diesel engine exhaust a very daunting task. Short term exposure to high concentrations of DE/DPM can cause headache, dizziness, and irritation of the eyes, nose, and throat severe enough to cause discomfort to miners and other workers. Prolonged DE/DPM exposure can increase the risk of cardiovascular, cardiopulmonary, and respiratory disease and lung cancer.
Regulations of Diesel Engine Exhaust – On June 6, 2005, the Mine Safety and Health Administration (MSHA) issued a final rule strengthening protections for miners exposed to diesel particulate matter (DPM) from diesel exhaust in underground metal and nonmetal mines.1
In June 2012, the International Agency for Cancer Research (IARC) classified DE (including DPM) as a known human carcinogen (Group 1). This re-classification was based on occupational health studies of workers exposed to high levels of diesel engine exhaust.
The Clean Air Act regulates a variety of source emissions. Overlapping networks of regulations also focus on diesel exhaust. The Occupational Safety and Health Administration (OSHA) and the Mine Safety and Health Administration (MSHA) enforce occupational diesel exhaust air contaminant regulations. Diesel emission exposure is regulated by MSHA for underground miners.2 In addition, MSHA requires the registration of diesel fuels with the EPA.
Miners are covered by MSHA while all other workers are covered by OSHA. MSHA currently enforces DPM standards at underground mines.3 For industrial mineral mines, a miner’s personal exposure to DPM must not exceed 160 micrograms per cubic meter (μg/m3) of total carbon (TC) when measured as an 8-hour time-weighted average. Engineering and administrative controls are required to reduce a miner’s exposure to at or below the permissible exposure limit (PEL). If these engineering and administrative controls do not reduce a miner’s exposure to below the PEL, then respiratory protection must be used to supplement these controls. Respiratory protection may include (1) air-purifying respirator equipped with a filter that is certified by NIOSH under 30 CFR Part 11 as a high-efficiency particulate air (HEPA) filter under 42 CFR Part 84 as 99.97% efficient or certified by NIOSH for DPM, or (2) non-powered, negative-pressure, air purifying, particulate-filter respirators shall use an R- or P-series filter or any filter certified by NIOSH for DPM. An R-series filter shall not be used for longer than one work shift. Rotation of miners to comply with the PEL is prohibited. It is necessary to evaluate a miner’s medical ability to wear a respirator and transfer rights for miners unable to wear respirators.
Other requirements include fueling practices, including sulfur content and fuel additives, maintenance of diesel-powered equipment, limits on engine emissions, annual training for miners, exposure monitoring, recordkeeping, and miners’ and former miners’ rights to access certain records related to their own exposures.
Engineering controls are the most effective strategy for minimizing worker exposure to DE/DPM. A combination of controls is often required. Examples include:
Administrative controls refer to changes in the way work tasks are performed to reduce or eliminate the hazard. Examples include:
Table I below provides detail about the levels of exposure in U.S. mines. The higher concentrations in underground mines are typically found in the haulage ways and face areas where numerous pieces of diesel equipment are operating, or where insufficient air is available to ventilate the operation. In surface mines, the average mean is almost half of the current standard with the higher concentrations typically associated with truck drivers and front-end loader operators.
The following section details a variety of solutions to controlling worker exposure to diesel particulate matter. These include both technology solutions as well as mine management procedures. Obviously, the first line of defense is using advanced technology to reduce the diesel particulate emissions in the first place.
Low Emission Engines: Low emission engines are produced by engine manufacturers to meet increasingly stringent Environmental Protection Agency (EPA) regulations. Benefits can be gained by replacing older model engines that require more maintenance with newer engines having lower emissions. Low-emission engines typically operate at high fuel injection pressures which provide more efficient and complete combustion of fuel. These engines are frequently turbocharged to optimize power, performance, and emissions. After-cooling (cooling intake air that is compressed and heated by the turbocharger prior to induction into the combustion chamber) is used to reduce oxides of nitrogen (NOx). Electronic engine control is another technological improvement, which optimizes the fuel-to-air ratio resulting in lower emissions.
Diesel Fuel: The quality of the diesel fuel influences emissions. Sulfur content, cetane number, aromatic content, density, viscosity, and volatility are interrelated fuel properties which can influence emissions. Sulfur content can have a significant effect on diesel particulate matter emissions. In addition, it affects sulfur oxide (SOx) emissions, all forms of which are harmful. Also, SOx emissions can poison catalytic converters, and the continued use of high sulfur fuel will contribute to increased piston ring and cylinder liner wear.
The Cetane number affects all regulated pollutants, and fuel aromatic content affects DPM and nitrogen oxides (NOx). Therefore, it is important to use diesel fuel with specific specifications and recommended property limits. Use of low sulfur diesel fuel (<0.05% sulfur) reduces the sulfate fraction of DPM emissions and allows oxidation catalysts to perform properly. Low sulfur diesel fuel is available nationwide due to EPA regulations.5
Fuel additives can also reduce emissions. Cetane improvers increase the cetane number of the fuel, which may reduce emissions. Another control technology is biodiesel fuels made from soybeans. This type of fuel contains about 10% oxygen, has a high cetane number, and a much higher flash point.
Exhaust Aftertreatment: Water scrubbers are basically a safety device used on equipment in underground mines. Water scrubbers perform three functions: (1) cool exhaust gases to safe temperatures, (2) arrest sparks and (3) arrest flames. The exhaust airflow from a diesel engine passes through water, making direct contact with the water. This direct contact with the water cools the air and quenches flames and sparks. Although not intended as an emission control device, scrubbers have been shown to remove about 30 percent of DPM from an engine’s exhaust stream. Water scrubbers themselves have no significant effect on gaseous emissions, but since water scrubbers cool the exhaust gases, they enable the equipment to be fitted with high efficiency paper filters that reduce DPM.
Exhaust Filtration: Exhaust filtration devices capture DPM from the exhaust before it enters the mine atmosphere. The most used exhaust filtration devices are disposable diesel exhaust paper filters and diesel particulate ceramic filters. Particulate control systems using these components typically remove 50 to 95 percent of the particulate.
Oxidation Catalytic Converters (OCCs): OCCs are used to reduce the quantity of carbon monoxide and hydrocarbons in diesel exhaust. Oxidation catalytic converters also decrease the soluble organic fraction of DPM as well as gas phase hydrocarbons, which can reduce DPM emissions by up to 50 percent.
Dry System Technology: An alternative to water scrubbers for meeting the exhaust gas cooling, spark arresting, and flame arresting requirements is the Dry System Technology (DST). With DST, the exhaust gas does not come into direct contact with cooling water, but it is indirectly cooled by a water-cooled heat exchanger such as a tube heat exchanger. The DST also includes a water-jacketed oxidation catalytic converter and a disposable diesel exhaust filter to reduce diesel emissions. This system reduces diesel particulate by 95 to 98 percent. The DST has been approved by MSHA under 30 CFR Part 36 for use in gassy mines.6
Mine Ventilation: The primary means used to reduce exposure to diesel exhaust pollutants underground is to dilute exhaust pollutants with fresh air from the mine’s ventilation system. The concentration of pollutants is inversely proportional to changes in ventilation air quantity. As the air quantity increases the pollutant concentrations decrease.
Mine ventilation systems where diesel engines are operated generally supply between 100 and 200 cubic feet of air per minute per brake horsepower (cfm/bhp). This air quantity is normally sufficient to dilute gaseous emissions from the diesel equipment to applicable standards for those gases. However, to significantly cause a reduction of DPM concentrations in underground mines through ventilation, it may be necessary to supply air quantities above those currently being used.
Enclosed Cabs: Properly designed and maintained environmentally conditioned booths can reduce equipment operators’ exposure to diesel emissions. Cabs should be pressurized and use high-efficiency particulate air (HEPA) filters.
Diesel Engine Maintenance: Engine maintenance is an important part of a mine’s strategy for reducing workers’ exposure to diesel emissions. Without proper maintenance, diesel engines will perform poorly, thereby reducing the effectiveness of all other emission control strategies.
Respiratory Protective Equipment: While it should not be used as the primary method of control, use of respiratory protective equipment can help to reduce miner exposure to DPM until better controls can be implemented.
Measuring DPM Concentration: Monitoring DPM concentrations is the ideal way for a mine to evaluate its progress in implementing a DPM control program. Mine operators can request help from MSHA’s Office of Technical Support on measuring or evaluating DPM exposures.
Training: Miners need to be properly trained. Miners must learn to recognize hazards, and to correctly operate and maintain diesel equipment. Designated maintenance personnel should be specially trained in diesel repair.
30 CFR § 57.5060 – Limit on exposure to diesel particulate matter.
Code of Federal Regulations, underground metal/nonmetal mines, https://www.ecfr.gov/cgi-bin/text-idx?SID=95a3589813c4b48d6daa8f8df80f0ead&c=ecfr&tpl=/ecfrbrowse/Title30/30cfrv1_02.tpl
METAL AND NONMETAL DIESEL PARTICULATE MATTER (DPM) STANDARD, Compliance Guide Q&As, Issued September 2006. https://arlweb.msha.gov/REGS/COMPLIAN/GUIDES/MNMDPM/MNMdpmcompguide.pdf
PRACTICAL WAYS TO REDUCE EXPOSURE TO DIESEL EXHAUST IN MINING, https://arlweb.msha.gov/s&hinfo/toolbox/dtbfinal.htm
ASTM D975 – 20c Standard Specification for Diesel Fuel, https://www.astm.org/Standards/D975.htm
Diesel Safety Component Certification Applications, 30 CFR 36, https://arlweb.msha.gov/techsupp/acc/application/asap3006.pdf